Zero Point Calibration in CNC Routing
by Ryan Dalton
Posted on 11-08-2023 02:18 PM
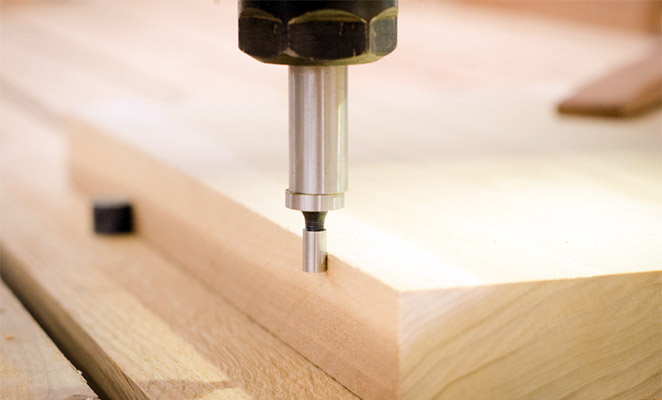
In the world of Computer Numerical Control (CNC) routing, achieving impeccable precision and optimal efficiency is paramount. At the heart of this quest lies the concept of Zero Point Calibration, a pivotal technique that forms the cornerstone of accurate machining processes.
Zero Point Calibration, often referred to as Zero-Point Alignment, is the meticulous process of establishing a reference point (also known as the "zero point") for a CNC machine's coordinate system.
This reference point serves as the foundation upon which all subsequent machining operations are based. The calibration ensures that the machine's movements are synchronized with the desired dimensions and positions, guaranteeing accuracy and consistency throughout the routing process.
Precision reigns supreme. The accuracy of the final product hinges on the machine's ability to adhere to the specified measurements with unfaltering consistency. This is precisely where Zero Point Calibration emerges as a game-changer.
By meticulously aligning the machine's coordinate system to a predefined reference point, manufacturers can eliminate deviations caused by mechanical tolerances and ensure that every cut, carve, and shape is executed with unparalleled accuracy.
The Calibration Process
1. Establishing the Reference Point
The first step in Zero Point Calibration involves defining the reference point of the CNC router machine. This point serves as the origin from which all measurements are calculated. It's crucial to choose a reference point that aligns with the specific requirements of the machining task.
2. Homing and Alignment
Once the reference point is set, the CNC machine undergoes a homing process. This entails moving the machine's axes to predefined limit switches, ensuring they are accurately positioned. Subsequently, the machine's axes are aligned to the reference point, guaranteeing that the machine's movements are in sync with the intended dimensions.
3. Compensation for Variations
Mechanical imperfections and thermal fluctuations can introduce variations in the machining process. Zero Point Calibration addresses these challenges by allowing operators to input compensation values. These values adjust the machine's movements to counteract potential errors, maintaining precision throughout prolonged operations.
Advantages of Zero Point Calibration
The adoption of Zero Point Calibration brings forth a multitude of advantages that elevate CNC routing to new heights:
1. Unparalleled Precision
Zero Point Calibration eradicates the cumulative errors that may occur due to variations in machine components. This results in parts and products that adhere faithfully to design specifications, minimizing rework and wastage.
2. Time and Cost Efficiency
The accuracy achieved through Zero Point Calibration diminishes the need for manual adjustments and refinements. This directly translates to reduced machining time, lower material wastage, and ultimately, a significant decrease in production costs.
3. Enhanced Workflow Consistency
Consistency is key in manufacturing, and Zero Point Calibration guarantees just that. With every routing task rooted in the same reference point, the potential for deviations and inconsistencies is virtually eliminated.
Zero Point Calibration Best Practices
To harness the full potential of Zero Point Calibration, consider these best practices:
1. Thorough Machine Inspection
Before calibration, conduct a comprehensive inspection of the CNC machine. Ensure that all mechanical components are in optimal condition to achieve the highest level of accuracy.
2. Regular Maintenance
Maintenance plays a pivotal role in preserving calibration accuracy. Regularly clean and inspect the machine's components to prevent wear and tear that could compromise precision.
3. Periodic Recalibration
Environmental factors and prolonged use can gradually affect calibration. Schedule periodic recalibration sessions to maintain consistent accuracy over time.
As CNC technology continues to evolve, embracing the power of Zero Point Calibration is a testament to a commitment to excellence in manufacturing.